BMW Motorenwerk Steyr: Wenn Rocky die schwere Last trägt
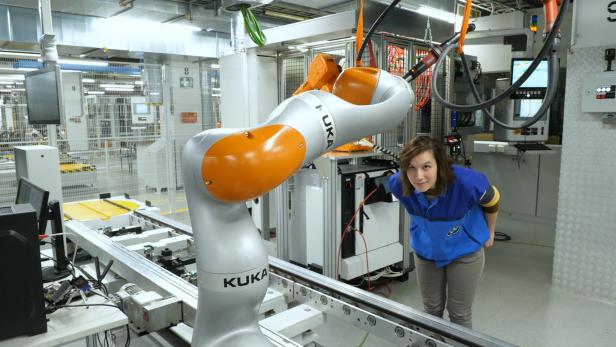
Autofahren wird mit Freiheit verbunden. Selbst zu entscheiden, wohin man sich bewegen möchte. Diese Individualität beginnt aber nicht erst mit Inbetriebnahme des Fahrzeugs. Sondern viel früher, beim Kauf. Ist ein Modell ausgewählt, muss noch zwischen zig Varianten in den diversesten Ausführungen entschieden werden. Zunächst meist der Antrieb: Diesel, Benzin oder gar schon Elektro? Diese zunehmende Individualisierung hat bei den Herstellern in der Produktion zu großen Veränderungen geführt. Wo es früher eine Handvoll Motorvarianten gab, sind es jetzt Hunderte. Der Einsatz digitaler Hilfsmittel soll dabei helfen, die Herausforderungen zu meistern.
Beispiel BMW Steyr: Im weltweit größten Motorenwerk des Münchener Autobauers werden 3-, 4- und 6-Zylinder Diesel- und Benzinmotoren in mehr als 400 Varianten hergestellt, darunter auch Motoren für Hybridantriebe.
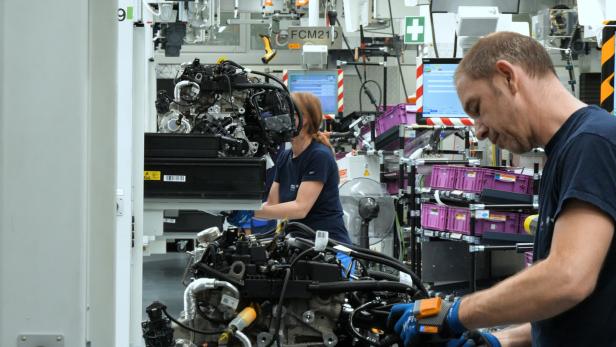
Um den Variantenreichtum bei den Antrieben zu beherrschen, werden unter anderem in Logistik und Produktion Datenhandschuhe verwendet. Daniel Grundwürmer, Leiter für Materialversorgung am Standort, demonstriert das Prinzip. Er steht vor bunten Plastikkisten, die mit vielen kleinen Teilen befüllt sind. Auf seinem Monitor sieht er, welche der Teile für den nächsten Motor benötigt werden. Flink sammelt er die Komponenten zusammen. Bevor sie in die Montage transportiert werden, gleicht Grundwürmer noch mithilfe des Datenhandschuhs ab, ob er die richtigen Teile beisammen hat. Wäre dies nicht der Fall, ertönt ein Warnsignal. Ähnliches geschieht ein Stockwerk tiefer beim Verbau der Komponenten.
1,5 Millionen Teile
Täglich werden durch 700 Mitarbeiter in der Logistik mehr als 1,5 Millionen Teile bewegt. Beim Transport von bis zu einer Tonne schweren Containern ist seit November ein selbstfahrender Roboter unterwegs, der von BMW entwickelt wurde. „Wir nennen ihn Rocky“, sagen die Mitarbeiter lachend. „Er macht das, was wir wollen.“ Kleinere Befehle könnten sie selbst programmieren. Rocky navigiert flankiert von Funksendern zur Vermeidung von Zusammenstößen und ausgestattet mit digitalen Karten durchs Werk. Im Endausbau soll es vier Rockys geben.
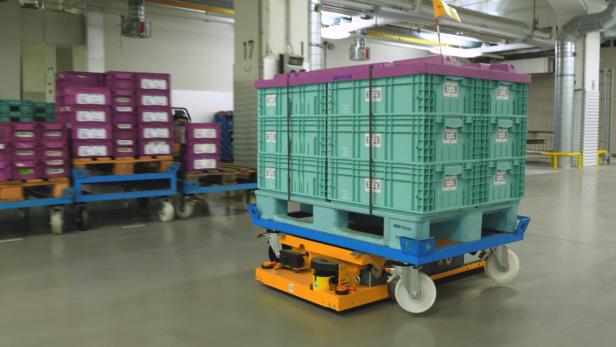
Roboter Rocky.
Nach Verbau der Motorenteile bleiben leere Container zurück. „Es gibt mehr als 400 Behältertypen“, sagt David Bricher, Mitarbeiter im InnoLab Steyr. Hier wird an der Digitalisierung der Produktionsprozesse, auch mithilfe von künstlicher Intelligenz, gearbeitet. Hier wurde auch die erste steuernde künstliche Intelligenz (KI) der BMW Group entwickelt.
Neuronales Netz
Ein neuronales Netz wurde mit Bildern von Leergutbehältern trainiert und erkennt, ob ein Behälter noch verzurrt werden muss oder nicht. Je nachdem nimmt das Leergut einen anderen Weg – zum Nachverzurren oder direkt zur Verladung. „Die Entscheidungen hat sich die KI selbst angelernt, die Logik dahinter wird ständig weiterentwickelt“, sagt Bricher.
Herzstück der Digitalisierung im Werk ist seit 2018 das InnoLab. „Hier werden Ideen der Mitarbeiter in Bezug auf Digitalisierung und KI im Produktionsprozess umgesetzt“, sagt Leiter Damir Bajrami. „Unser Team besteht aus acht Mitarbeitern und setzt sich interdisziplinär mit Programmierung, Steuerungstechnik und Design auseinander.“ Auch mit Hochschulen gibt es bereits Kooperationsprojekte.
InnoLab-Leiter Bajrami (Teil1)
Seit knapp einem Jahr wird an einem mitdenkenden Leichtbauroboter gearbeitet. Dieser soll bei der Zusammenarbeit mit Menschen auf diverse Körperteile unterschiedlich reagieren. „Kommt etwa der Kopf des Mitarbeiters dem Roboter zu nahe, stoppt er sofort. Bei einer Hand wird er nur langsamer“, erklärt Bajrami. Durch eine Kamera erkennt der Roboter die Gliedmaßen und passt seine Geschwindigkeit entsprechend an. Der neuartige Roboter soll laut Bajrami „in absehbarer Zeit“ in Betrieb genommen werden.
InnoLab-Leiter Bajrami (Teil2)
Mittlerweile beträgt der Automatisierungsgrad in der Mechanischen Fertigung in Steyr bereits 98 Prozent. Trotzdem sind hier die meisten Mitarbeiter – mehr als 1.200 – beschäftigt, hauptsächlich mit der Programmierung, Bedienung und Instandhaltung. „Mithilfe von Data Analytics sehen wir Störungen unserer Anlagen vorher, bevor sie überhaupt entstehen“, sagt Werner Schröder, Leiter Instandhaltung. „Sensoren innerhalb der Anlage nehmen verschiedenste Betriebszustände wie Frequenzen, Motorströme und Temperaturen wahr. Auffälligkeiten werden unmittelbar kontrolliert.“ Auch in der Motorenmontage übernehmen Roboter schwere und monotone Tätigkeiten, wie zum Beispiel Verschraubungen.
Werkschef Christoph Schröder sieht naturgemäß im hohen Digitalisierungsgrad keine Bedrohung für die Mitarbeiter. „Sie sind hoch qualifiziert“, sagt er im KURIER-Gespräch (siehe Videos).
Christoph Schröder im Gespräch (Teil1)
Christop Schröder im Gespräch (Teil2)
Nachgefragt
KURIER: Würden Sie Ihr Werk als Fabrik der Zukunft bezeichnen?
Christoph Schröder: Ob wir schon die Fabrik der Zukunft sind, weiß ich nicht. Aber auf alle Fälle sind wir eine Fabrik mit Zukunft (lacht). Wir haben alleine im letzten Jahr 308 Millionen Euro investiert, davon einen Großteil in Digitalisierung.
Geht es noch ohne Digitalisierung?
Nein. Die moderne Produktionswelt ist ohne Digitalisierung nicht mehr vorstellbar. Wir haben sehr viele Fahrzeugmodelle und mehr als 400 Motorvarianten. Diese Komplexität ist ohne Digitalisierung nicht darstellbar. Auch all unsere Anlagen sind miteinander vernetzt.
Zukunftstechnologie heißt bei Motoren auch Elektroantrieb. Sehen Sie da auch Zukunft in Ihrem Werk?
Natürlich, wir haben ja bereits begonnen mit den Elektroantrieben. Wir entwickeln und fertigen Gehäuse für Elektroantriebe und erproben Kühlkreisläufe oder hochkomplexe Komponenten wie Ladekabel bei uns am Standort. 40 Prozent aller Motoren für Hybridantriebe kamen alleine 2018 aus Steyr.
Im Werk gibt es viele Roboter. Werden dadurch über kurz oder lang die Mitarbeiter wegrationalisiert?
Ich glaube nicht. Auch in Zukunft haben wir hier keine menschenleere Fabrik, sondern hochqualifizierte Mitarbeiter, die diese Anlagen managen.
Kommentare